Gas Company filters play an important role in the purification and purification of natural gas. These filters remove pollutants such as dust, moisture, rust particles and other solid impurities from the gas, thereby ensuring the safe and optimal performance of gas supply equipment. In this article, we examine the types of gas filters, how they operate and their importance in the gas industry.
The importance of filtering in gas systems
Natural gas passes through a variety of paths before reaching consumers, with the possibility of unwanted particles being introduced into the gas flow. The entry of these pollutants can damage equipment, pipes and gas turbines, reducing efficiency, increasing maintenance costs, and even safety risks. Therefore, it is necessary to use appropriate filters in gas lines.
Types of gas filters
filters used in the gas industry are divided into several categories by type of performance and location:
Filters of the Sphere
These filters are specifically designed to remove moisture and liquids from natural gas. Their function is mechanical separation in which the liquid droplets are separated from the gas and collected at the bottom of the tank.
Cartridge filters
These filters are used to absorb solid particles in the gas. The filters are usually made of polypropylene or high absorption fibers, which cause even the fine particles to be removed from the gas.
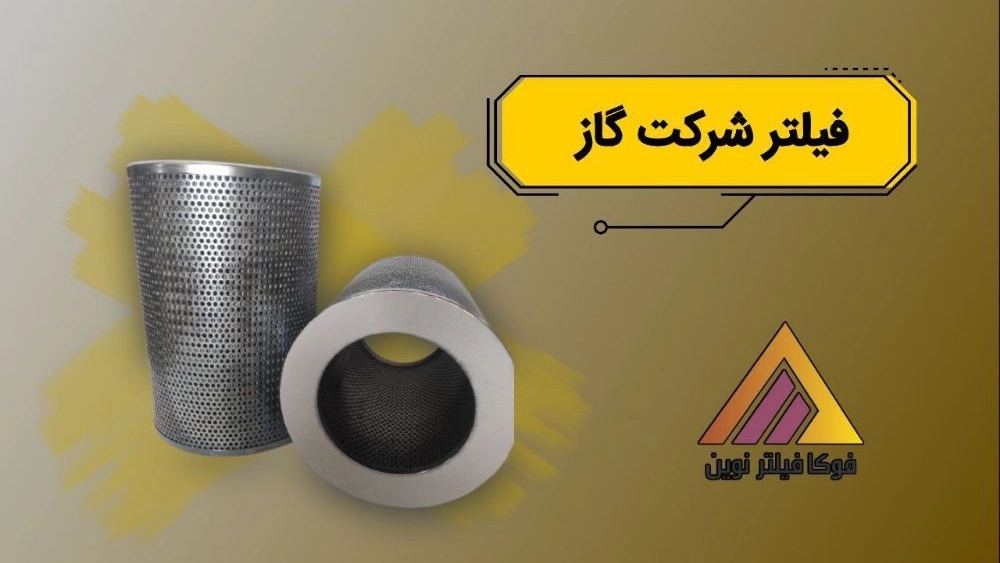
Lattice filters
These filters are usually made of metal mesh and are used to separate larger particles in high pressure lines.
Molecular filters
These filters have a porous structure and are used to absorb specific molecules such as moisture and sulfur compounds.
How gas filters work
Gas filters are usually installed in the gas flow path and remove existing pollutants using mechanisms such as mechanical, electrostatic or absorption. The performance of each filter depends on the type of design, the amount of gas discharge and the size of the particle.
The benefits of using gas filters
• Extension of equipment life: removal of solid particles and liquids from gas reduces erosion and corrosion in the equipment.
• Improvement of System Performance: Use appropriate filters Improves the performance of turbines, compressors and heat exchangers.
• Reduce maintenance costs: Preventing harmful particles from entering the gas lines reduces equipment maintenance costs.
• • • • • • • • • • • • • • • • • • • • • • • • • • • Increase safety: Removing combustible and corrosive contaminants can reduce the risk of explosion and damage to gas infrastructure.